Nichols College News
Nichols College’s Public Relations team is available to help members of the media with questions and stories, conducting interviews on campus, and photo requests. If you’re a member of the media seeking information about Nichols College, a faculty or staff member or a student, we ask that you arrange interviews and on-campus photos through the Public Relations office.
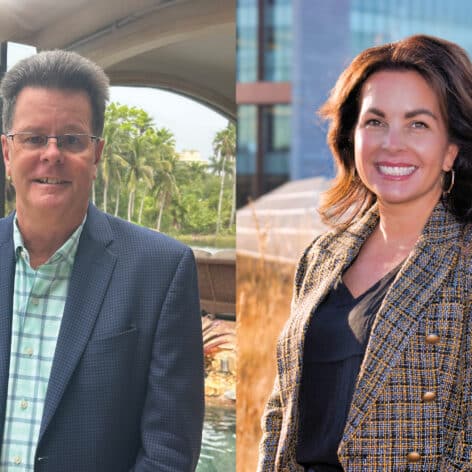
Nichols College board elects new chair, vice chair, trustees
July 3, 2025
DUDLEY, Mass. – At its May 2 meeting, the Nichols College Board of Trustees elected David G. Bedard as the new chair and Jaime Paris Boisvert as the new vice chair of the 27-member board. During the academic year, the board also elected Edmond J. (E.J.) Landry and Taylor Cornell as new trustees. Bedard is […]
Read More about Nichols College board elects new chair, vice chair, trustees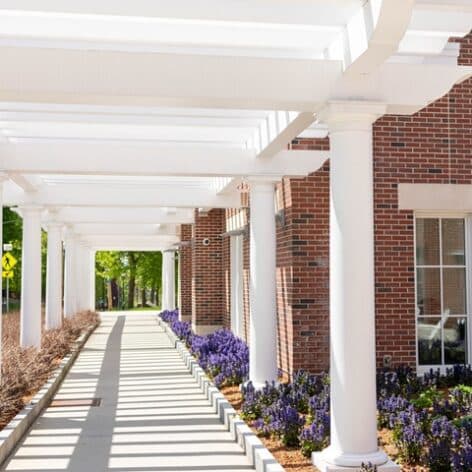
Nichols College announces President’s and Dean’s Lists for spring 2025
June 24, 2025
DUDLEY, Mass. – Nichols College is pleased to have named more than 440 students to the President’s and Dean’s Lists for the spring 2025 semester. The Dean’s List and President’s List give recognition to those students who achieve high grades during a single semester. To be included on the Dean’s List, a student must have […]
Read More about Nichols College announces President’s and Dean’s Lists for spring 2025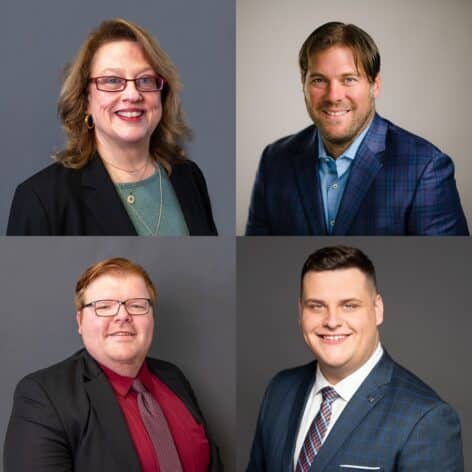
Nichols College names Brothers, Darling, Hoey and Maymon to its Board of Advisors
June 5, 2025
(New Board of Advisors members, left to right, top to bottom: Lynn Brothers, Michael Darling, Patrick Hoey, Jared Maymon) DUDLEY, Mass. – Nichols College has named four new members to its Board of Advisors (BOA). The BOA is an engaged volunteer leadership body that lends its time, talent and resources to support the strategic initiatives […]
Read More about Nichols College names Brothers, Darling, Hoey and Maymon to its Board of Advisors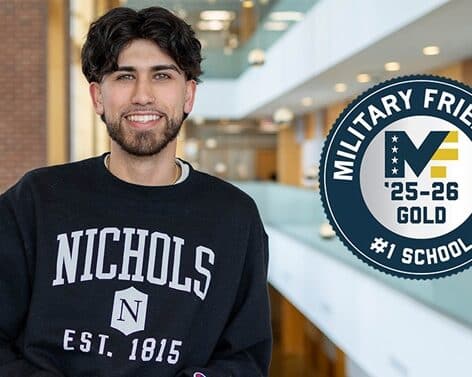
Nichols College named a 2025–26 Top 10 Military Friendly® School
May 21, 2025
DUDLEY, Mass. – Nichols College was recently named a top Military Friendly® School, achieving the No. 1 ranking and Top 10 status among private institutions that do not offer a doctoral degree. The ranking reflects an improvement over last year’s Gold Level status—itself a notable achievement—and signifies that Nichols is a national leader in supporting and […]
Read More about Nichols College named a 2025–26 Top 10 Military Friendly® School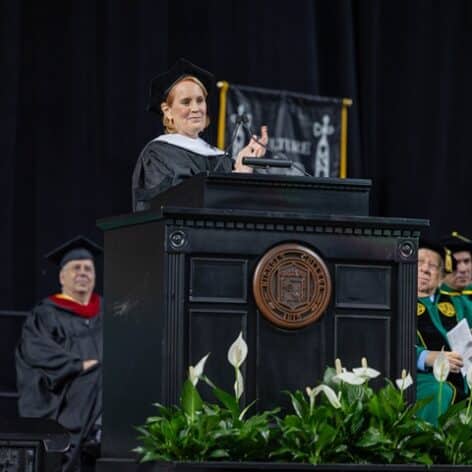
“Don’t be afraid to say yes,” BlackRock’s Anne Ackerley tells Nichols graduates
May 3, 2025
DUDLEY, Mass. – Anne F. Ackerley, a senior advisor to the retirement business at BlackRock and previously the head of BlackRock’s U.S. Retirement Group, shared lessons from her life and career as she delivered the commencement address during the Nichols College commencement ceremony on May 3, 2025. A total of 412 students participated in the graduation […]
Read More about “Don’t be afraid to say yes,” BlackRock’s Anne Ackerley tells Nichols graduates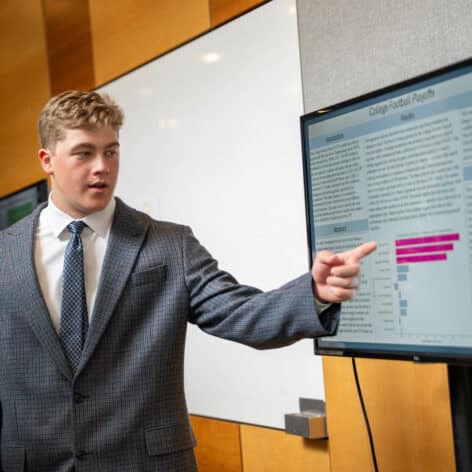
Nichols holds third annual REAL Symposium
April 23, 2025
DUDLEY, Mass. – “Capture this moment as an opportunity,” said Nichols College alumna Kelly Bliss ’96, president of Teladoc Health’s U.S. Group Health (USGH) business, during her keynote address opening the College’s third annual Research, Experiential, and Applied Learning (REAL) Symposium. The REAL Symposium is a day-long event celebrating the many unique and impactful projects […]
Read More about Nichols holds third annual REAL Symposium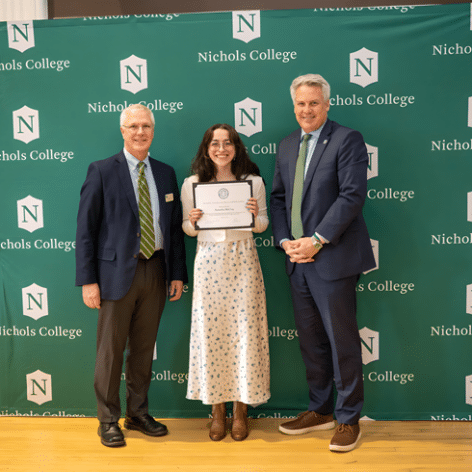
Academic standouts honored at Nichols awards ceremony
April 16, 2025
DUDLEY, Mass. – Nichols College celebrated academic excellence and student achievement during its annual Academic Awards Ceremony on Tuesday, April 15. Held on campus, the event recognized students across a range of majors for their hard work in the classroom, dedication to their fields and contributions to the Nichols community. Honors included department awards, endowed […]
Read More about Academic standouts honored at Nichols awards ceremony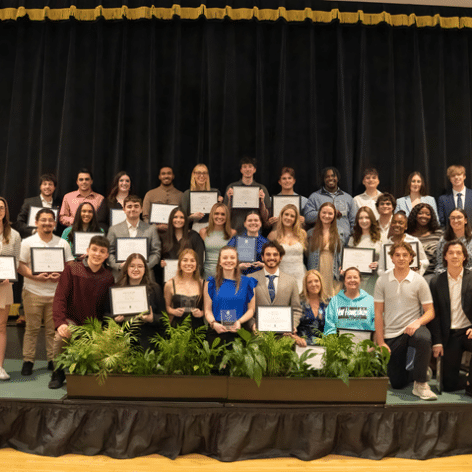
Student leaders shine at Nichols annual awards ceremony
April 16, 2025
DUDLEY, Mass. – Nichols College recognized outstanding student leaders during its annual Student Leadership Awards ceremony on Tuesday, April 15. The event spotlighted students and organizations making a difference on campus—whether by leading standout programs, creating a more inclusive community, or going above and beyond in their roles. Honors included the Bison Excellence and Legacy […]
Read More about Student leaders shine at Nichols annual awards ceremony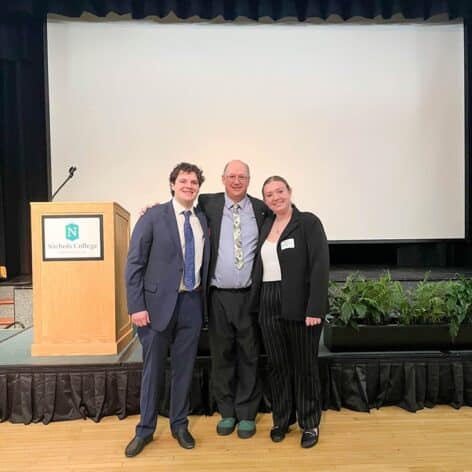
Nichols students to represent College at WooTank pitch competition
April 4, 2025
From elevator pitches to Shark Tank style competitions, Nichols student innovators are working to turn big ideas into real opportunities. Two of those innovators, Mackenzie Masters ’28 and Giovanni Cucco ’27, will represent Nichols College at the WooTank Intercollegiate Showdown on Tuesday, Apr. 8 from 5–8:30 p.m. at Off the Rails in Worcester, Massachusetts. Hosted […]
Read More about Nichols students to represent College at WooTank pitch competition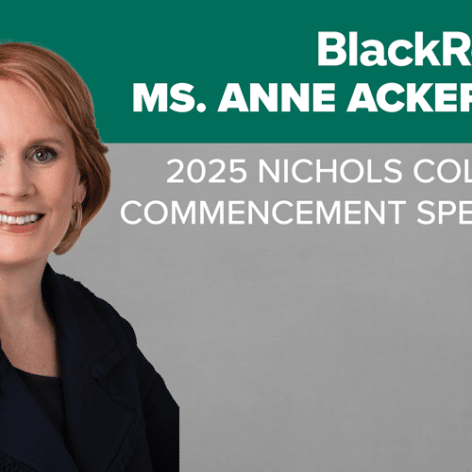
Anne F. Ackerley, senior advisor at BlackRock, to deliver Nichols College commencement address
March 18, 2025
Nichols College has announced that Anne F. Ackerley, senior advisor at BlackRock, will give the Commencement Address at the 2024 commencement exercises on Saturday, May 3.
Read More about Anne F. Ackerley, senior advisor at BlackRock, to deliver Nichols College commencement address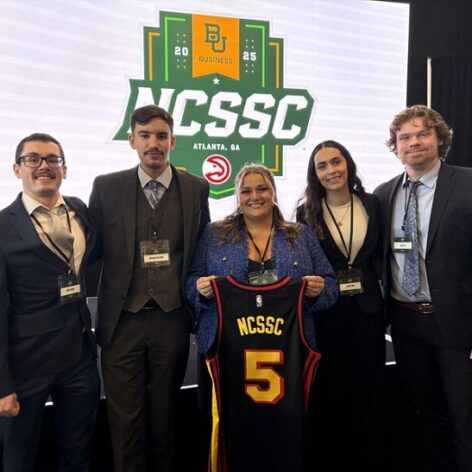
Nichols student finishes top 5 nationally in sports sales championship
March 11, 2025
Nichols College sport management students made an impressive showing recently at the National Collegiate Sports Sales Championship (NCSSC) in Atlanta, with standout competitor Jillian Archer ’25 placing fifth nationally in the ticket sales division. The academic competition, held at State Farm Arena, featured students from over 50 colleges and universities, testing their ability to pitch […]
Read More about Nichols student finishes top 5 nationally in sports sales championship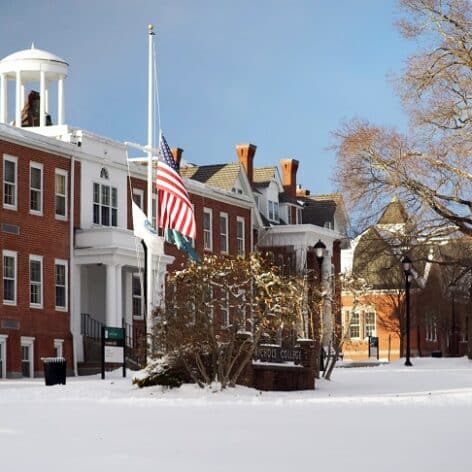
Nichols College announces President’s and Dean’s Lists for fall 2024
January 23, 2025
DUDLEY, Mass. – Nichols College is pleased to have named more than 480 students to the President’s and Dean’s Lists for the fall 2024 semester. The Dean’s List and President’s List give recognition to those students who achieve high grades during a single semester. To be included on the Dean’s List, a student must have […]
Read More about Nichols College announces President’s and Dean’s Lists for fall 2024